- Alaska
- Arizona
- Arkansas
- California
- Delaware
- Hawaii
- Kentucky
- Louisiana
- Maryland
- Missouri
- New Jersey
- Ohio
- Pennsylvania
- Texas
- Utah
- Washington, D.C.
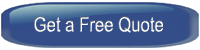
IFT Featured Louisiana Job
Dual HDPE Pipe Linestop + Bypass Services
Job Status: Successful and Completed Job Date: February 7, 2014 PROJECT: Linestops and Bypassing HDPE Pipeline Click for a Short Cut to content using the links below Coupon Retention & IFT – T-46 Tapping Machine Hot tap "Coupon" Retention and Removal JCM - Generic Fitting Specification for HDPE Hottap & Linestop Linestop with Bypass – Photo / Inside Isolated Pipeline - Photo Description of Linestop™ Sequence Generic Specification HDPE – (DR-26) Linestop Removal of Temporary Valves Using Completion Flanges & Plugs International Flow incorporates multiple retaining wires to provide retention of coupon.The majority of our Hot tapping is performed vertically "on top" of the pipeline.Thus retaining the cut section or "coupon" is critical. Performing 24" Hottaps for retention safety requires a minimum of (4) sets of retaining wires to pass through the pipe section prior to the tapping cutter completing the tap. This safeguards the coupon from being lost into the system. ![]() T-46 Tapping Machine 46" of travel performs 12" - 24" Taps ♦ Travel can be increased if desired to 60" with "T46-60 Rail and Boring-bar" ♦ Very Powerful Built in drive unit ♦ Tapping machine is hydraulic driven: 16 gallons at 2000 psi. is preferred. ♦ Machine has patented "Selectable-feed" ♦ 3" Boring Bar for ridged cutting. ♦ Gear driven for precision cutting and dependability ♦ Dual Hydraulic motor drive for non-stop cutting ♦ Mueller style cutters bolt up with use of an adapter ♦ 285 psi. working pressure with quoted adaptors. ♦ 285psi & 250 degrees (F) with provided packing. ♦ Higher Temperatures are available with optional packing. ♦ American std & British std, adaptors ♦ Operating max. pressure 285 psi. @ 100º F ♦ Operating temperature 250º @ 300º psi.
Cutting HDPE Is performed with sharp and fluted cutters. The pilot Drill performs the retention of the Cut section or "coupon" allowing it to be removed under pressure. JCM 452 Fabricated Linestop Sleeve – All Stainless Steel Gasket: Nitrile Butadiene Rubber (NBR, Buna-N) per ASTM D2000. Molded virgin rubber with a pressure activated hydromechanical design. Gasket is bonded into a cavity for internal and external retention. Gasket temperature range -40oF to 212oF (-40oC - 100oC) Gasket suitable for water, salt solutions, mild acids, bases, and sewage. Optional gasket materials available. Fitting Flange: Stainless steel, 18-8 Type 304. Bolts: Stainless steel, 18-8 Type 304. Blind Flange: Fusion epoxy coated Ductile Iron. Blind Flange: Fusion epoxy coated A-36 Ductile iron. Service Rating: 12" to 24" Outlets: 150 PSI. A Bypass is installed between the Linestopping machines.
HDPE PIpe is Generally smooth inside so many times Bubble tight Linestop Shudowns are common making it easy for the contractor to perform their work. LineSTOP® Specifications for HDPE Pipe (150 PSI OR LESS) Description of Procedure - The line stopping procedure is a means of temporarily plugging a pressurized pipe without disrupting pressure of service upstream of the line stop. A pressure tap is first made into the main, allowing insertion of the linestop device into the main under pressure. By using a special line stop fitting, the tapping valve can later be recovered after the plugging head has been removed from the main. NOTE: Because of expansion and retraction of HDPE it is suggested that mechanical connections be made using the following in mind. "If pipelines are on top of the ground and encounter more than a 10-degree temperatures fluctuations, you may see problems and may have to install a mechanical tee or fuse the connection". 1. Prior to ordering material: Excavate, dewater excavation, expose and clean the exterior of the main at the location of the linestop®. If main is heavily corroded; or if utilities will interfere with fittings, support/thrust blocking, or equipment; move location up or downstream to structurally sound pipe. a. On pipelines 14" and larger; it may be necessary to Caliper O.D. of mains to determine ovality. b. Verify wall thickness by stated SDR # or by hot tapping techniques and/or ultrasound methods. c. Backfill; restore as requested by Owner. 2. Re-excavate; dewater. Assemble Linestop® fitting(s) around the main. Install drain nozzle(s) and saddle(s) to then main. According to the HDPE manufacturers information, cutter size should be no larger than 90% of the pipe I.D. (Pipe O.D. ÷ SDR#= gives wall thickness x 2 walls=I.D.) 3. Pressure test per Engineer’s specifications. 4. Pour concrete support and thrust blocking. Allow curing per Engineer’s instructions. 5. Mount temporary tapping valve(s) to linestop® fitting(s). 6. Mount tapping machine; open valve; pressure tap; retract cutter with coupon; close temporary valve; remove tapping machine. 7. Mount International Flow Technologies, Inc. linestop® machine; open temporary valve; insert linestop® plugging head into main. a. If two or more linestops, insert downstream plugging headfirst. b. "Flow must be stopped momentarily while heads are inserted" 8. Test for shutdown at drain nozzle. 9. Cut downstream main. Install required fitting(s) and valve(s). 10. Equalize section of pipe through drain nozzle. 11. Remove linestop® equipment. 12. Install the completion machine; set completion plug; remove temporary valve(s); install blind flange(s). Drain Nozzles - Because some amount of leakage may pass linestops, a drain tap of 2" or greater shall be added to the line to determine the quality of the shutdown. 1. Contractor shall have the option of recovering the drain valves by using linestop® type tapping nozzles with completion plugs or abandoning the valves by leaving them attached to the nozzles. In either case, the outlet of each nozzle or valve shall be sealed with a blind flange, mechanical joint plug, or screwed pipe cap or plug. 2. The drain-tapping fitting shall consist of a saddle plate with an integral flanged nozzle to which a tapping valve can be attached in a pressure-tight manner. a. The interior of the saddle plate, adjacent to and concentric with the O.D. of the nozzle, shall be grooved to retain a gasket, which shall seal the saddle plate to the exterior of the HDPE/DI main. This gasket shall constitute the only seal between the main and the fitting. b. Saddle shall be clamped to main by minimum of two "U" shaped stainless steel strap/stud assemblies of sufficient cross section to contain a line pressure of 200 psig. Extent of Shutdowns - The shutdown will be accomplished by using a linestop®. Because of possible, out-of-roundness in the main, "bottle-tight" shutdowns may not occur. A satisfactory shutdown is one, which allows the work to be accomplished (i.e. valve installation) using drainage pumps to dewater if needed. Preliminary Field Inspection of Mains - Dimensional, specification, and other data regarding the existing mains have been taken from pipe data. 1. Prior to ordering material, Owner shall excavate at each proposed location, take an O.D. reading and caliper the header diameter to determine ovality. a. If I.F.T. determines that data on pipe I.D. is not adequate I.F.T. may make one or more pressure taps on main to determine I.D. from coupons. b. Minimum size of test coupon shall be 1 7/8" diameter, drilled through a nominal 2" valve. Line Stop Fitting and Accessories - Fitting shall be a fabricated type split tee. It shall consist of two steel weldments; (1) an upper line stop flange saddle plate and (2) a lower saddle plate. These two saddle plates shall be continuous. 1. Line Stop Flange: The outlet of each fitting shall be machined from a 150 lb. Stainless steel plate (304). Flat faced and drilled per ANSI B16.5. Suitable independently operated locking devices shall be provided in the flange to secure the completion plug. 2. Line Stop Nozzle: The nozzle, which lies between the saddle and the flange, shall be fabricated from 304 stainless steel pipe. After welding and stress relief, the nozzle shall be accurately bored to accommodate the line stop plugging head. 3. Fasteners: All bolts, studs, and nuts used on line stop and drain equalization fittings shall be machined from Type 304 stainless steel. 4. Gaskets: Shall be molded form elastomer compounds that resist compression setting and are compatible with water in the 32 degree to 140 degree temperature range. Installation of Linestop® Fittings - Line stopping Contractor shall clean the exterior of the main to remove any debris, corrosion deposits, or other surface irregularities that might interfere with proper seating and sealing of each linestop® fitting against each main. Any structural defects in main, service connections, appurtenances, adjacent utilities, etc., that could interfere with the line stop installation shall be immediately reported to the owner. 1. Line stopping Contractor shall fit upper and lower saddle plate assemblies to main, thoroughly checking for proper fit to main. 2. Under no circumstances shall Contractor attempt to force, reshape or bend saddle plates by excessive tightening of saddle studs while linestop® fitting is assembled around the main. a. Any retrofitting shall be accomplished with the fitting removed from the main. Thrust Support and Blocking - Prior to mounting temporary tapping valve and pressure tapping machinery, Contractor shall install concrete thrust and support blocking specified by Engineer. Blocking shall reach a minimum core strength specified by Engineer before any valves or machinery shall be mounted onto the linestop® fitting. Cutting Operation - Drilling equipment shall be in good condition and equipped with the power drive to ensure smooth cutting, and to minimize shock and vibration. Cutting equipment shall be sharp and have a coupon retention device in the pilot drill suitable for retaining the size of the coupon to be cut. REMOVAL OF IFT TEMPORARY LINESTOP® VALVES
Once the pipe
modifications are completed, the temporary bypass and Linestop machines are
removed. IFT’s completion tool holds and installs a completion plug into the
neck of the fitting to isolate the product from the temporary isolation valves. Future reentry of Linestop machinery can be performed by reversing this procedure. IFT Completion Plug Assemblies
Completion plug assemblies come in many different styles IFT completion plugs for pressures through 300 psi. use a pin type flange. The inside threaded hole holds retainer pin which threads into the top groove of the completion plug. The outside thread is tapered to match a pipe plug that seals the pin assembly.
The completion plug fits into the flange and seals with an O-ring against the inside of the nozzle. The plug is held in place by the pin assembly that is installed from the outside with an allen wrench. Typical
Completion Plug Assembly |
||
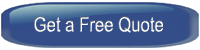