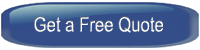
Wall / Tank / Concrete Vessel / Cylinder Tapping Services:
Tap Sizes:Our wall tapping assemblies are used for hot tapping onto concrete walls, concrete storage tanks, and large diameter concrete conduits, where a backing draw plate is impractical. We manufacture any size contour to match your needs, with any size outlet through 120", in 125, 150, and 300 lb. classes. The body is fabricated from carbon steel and is available in shop coat or fusion epoxy coat, with either shop coated, fusion epoxy lined, or mortar lined waterways. The assembly is fabricated to match the existing wall contour. Our stainless steel anchor bolts are used to attach the tapping outlet securely to the wall. For smooth walls, one Q-Ring seal is adequate, though for extra security two Q-Rings seals can be used. All assemblies include stainless steel anchor bolts, and a carbide drill bit structure for drilling the concrete structure.
Any wall thickness can be tapped. 20' thick or thicker have been performed.
Our patented Square Flange products allow: the Hot Tapping of Butterfly Valves and Plug valves; and can “leave no valve” after the connection.
Get a quote for your indoor, outdoor, underground or above, wall tapping needs
Call 1-800-221-3332
Hot Tapping Procedures For Concrete Walls and Tanks
In preparation of a wall tap, the surface on the existing wall should be pre- excavated, and inspected, prior to ordering the tapping anchor and seal plate. In most circumstances the wall surface should be flat and have no visible signs of cracking. If the surface is not smooth, or slight deformations exist on the wall surface, a diamond surface grinder can be used to smooth surface. Smooth grinding will improve the surface condition to ensure a gasket seal. If the wall has visible signs of cracking it is possible to seal the cracks, but choosing a different location may prove to be more practical.Once the connection point is inspected the anchor plate can be ordered. When ordering the anchor plate, please specify either, shop coating, fusion epoxy coating, or stainless and grade. Also indicate the type of anchor bolts, "low alloy" or "stainless steel." For installation to the wall, holes are provided through the anchor plate to allow the anchor bolt to be drilled into the wall with nuts that draw the anchor plate tight against the wall. Chemical adhesion of the anchor bolts is preferred by IFT. Once the bolts, anchor plate and nuts are installed, the gasket compresses against the wall surface to create a permanent seal.
After the anchor plate installation is complete, the tapping valve shall be installed, and the valve bolts shall be tightened in a star alternate pattern, so the valve will mount flush. For valves 8" and larger, a permanent valve support is recommended. At this time the tapping machine will be installed and the anchor plate, tapping valve, and tapping machine will be pressure tested 25% over the working pressure, with a hydrostatic test-pump.
Upon a successful test the tapping cutter of the hot tapping machine will be advanced forward and the wall will be hot tapped. Once the hot tap is complete, the shell cutter is retracted, and the tapping valve will be closed. At this time the tapping machine is removed and piping can be installed.
Because of the cut-ability of most concrete, connections can be made at many angles into the wall. The connection can be made at an angle such as 45 degrees into the wall. This is considered an "angle tap". Also, very thick walls can be tapped by means of making several preliminary penetration cuts, removing the cutter and tapping machine, chipping away and cleaning out the area within the cut section, and reassembling the tapping machine to continue making the cut. (Repeating this procedure if needed). When the desired depth is achieved by the preliminary tapping, a final cut will be made to complete the live connection.
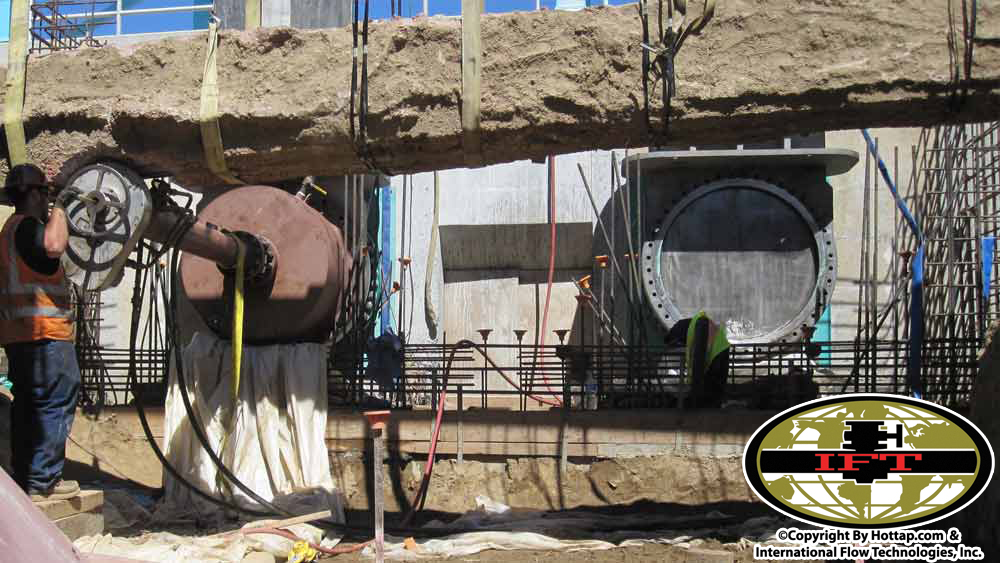
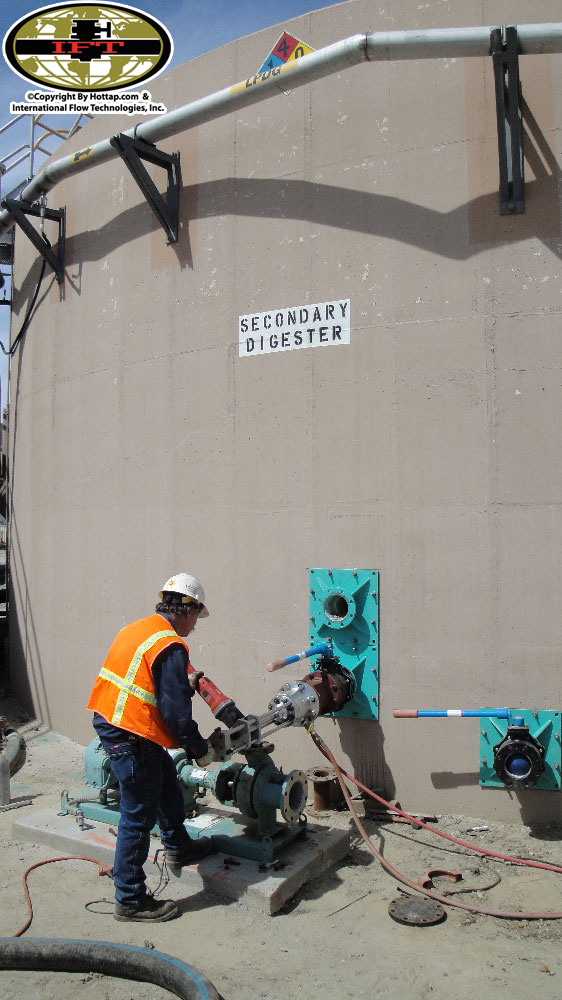
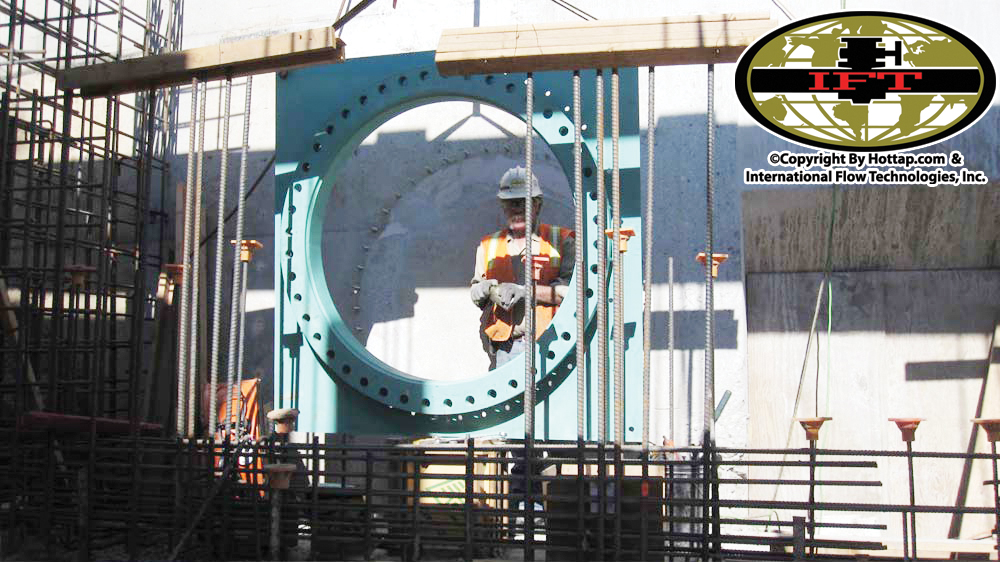
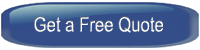